Opening the Potential of Aluminum Spreading: Proven Methods for Success
Light weight aluminum casting has long been acknowledged for its versatility and extensive applications throughout numerous industries. Join us as we explore the crucial elements that can push light weight aluminum spreading towards exceptional success in today's affordable market landscape.
Benefits of Light Weight Aluminum Casting
Aluminum casting supplies a multitude of advantages that make it a favored selection in numerous commercial applications. Among the primary advantages of light weight aluminum spreading is its light-weight nature, which adds to sustain efficiency in industries such as vehicle and aerospace. In addition, aluminum is highly malleable, allowing for complicated and complex shapes to be quickly produced with casting processes. This adaptability in layout is a significant benefit for sectors that call for parts with details geometries.
Furthermore, aluminum spreading supplies outstanding corrosion resistance, making it perfect for applications where exposure to rough atmospheres is an issue. The material additionally displays good thermal conductivity, which is beneficial for sectors needing heat dissipation, such as electronic devices (about aluminum casting). In addition, aluminum is totally recyclable, lining up with the growing emphasis on sustainable practices in modern-day manufacturing.
Layout Considerations for Casting
The style stage plays a vital duty in the overall success of a light weight aluminum spreading job. One crucial consideration is the option of proper geometries and attributes that help with the casting procedure.
Furthermore, considerations associated to parting lines, gating systems, and risers are necessary to avoid flaws like porosity and contraction. It is crucial to optimize the style for effective product use and decrease post-processing requirements. Simulations and prototyping can be important tools in examining and improving the spreading design before full-blown production.
Partnership in between style manufacturers, engineers, and shops is important to attend to any type of prospective challenges early in the design stage. By integrating these considerations into the spreading layout procedure, makers can improve product top quality, lower expenses, and ultimately unlock the complete potential of light weight aluminum spreading.
Enhancing Casting Effectiveness
When aiming to improve casting efficiency in light weight aluminum casting jobs,Designing with an emphasis on optimizing material circulation and reducing issues is necessary. To achieve this, making use of simulation software application can aid in determining possible issues prior to the spreading process starts. By mimicing the circulation of molten aluminum, developers can readjust gating and riser designs to make sure proper dental filling and solidification, ultimately decreasing the event of problems such as porosity or shrinking.
Moreover, executing appropriate warmth treatment processes can improve the total casting effectiveness. Warmth therapy can help improve the mechanical buildings of the aluminum casting, making sure that the last component satisfies the called for requirements. Additionally, using automation and robotics in the casting process can improve manufacturing, minimize manual work, and increase overall efficiency.
In addition, continuous monitoring and high quality control during the casting process are important for determining any type of deviations and guaranteeing that the final products meet the desired standards. By executing these methods, makers can improve casting effectiveness, improve product quality, and inevitably attain better success in light weight aluminum spreading tasks.
Quality Assurance in Light Weight Aluminum Casting

Effective quality control practices play an essential function why not check here in making certain the precision and dependability of aluminum spreading processes. Quality control steps in aluminum spreading incorporate an go to this site array of tasks aimed at supporting details standards and identifying deviations that could endanger the last product.
In addition to procedure control, quality assurance in aluminum spreading includes rigorous testing and inspection treatments at different stages of manufacturing. Non-destructive screening techniques like ultrasonic testing and X-ray inspection aid find interior problems without compromising the honesty of the actors elements. Visual inspections, dimensional dimensions, and mechanical testing further make certain that the cast parts satisfy the called for specs and performance requirements. By executing durable high quality control methods, light weight aluminum spreading facilities can supply products that fulfill client assumptions for quality, efficiency, and reliability.
Making The Most Of Earnings
To attain optimum economic performance, an extensive strategy for maximizing productivity within light weight aluminum casting operations have to be thoroughly created and carried out. One essential aspect of maximizing productivity in aluminum spreading is enhancing production performance.
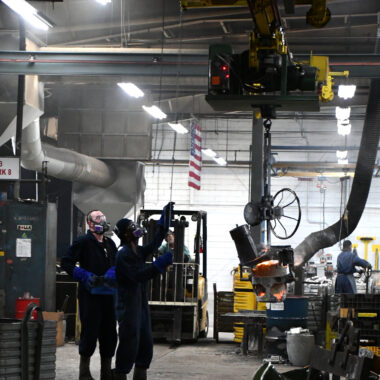
Moreover, expanding item offerings and checking out new markets can help expand revenue streams. Comprehending consumer needs and market patterns can assist calculated decisions to YOURURL.com profit from emerging opportunities. Buying study and growth to introduce procedures or items can likewise drive earnings with differentiation and consumer satisfaction.
Conclusion
Finally, light weight aluminum casting offers countless benefits in terms of layout flexibility, resilience, and cost-effectiveness. By very carefully considering layout considerations, enhancing casting effectiveness, implementing top quality control steps, and taking full advantage of profitability, makers can open the complete possibility of aluminum spreading. This versatile and trustworthy process has confirmed to be an effective option for a wide array of industrial applications.
Furthermore, light weight aluminum is highly malleable, permitting for detailed and complex shapes to be quickly created via casting processes.Effective top quality control practices play an essential duty in guaranteeing the precision and dependability of light weight aluminum spreading processes.In addition to process control, high quality control in light weight aluminum spreading involves rigorous testing and evaluation procedures at different phases of manufacturing. By carrying out robust quality control methods, aluminum casting facilities can provide products that satisfy client assumptions for efficiency, integrity, and high quality.
By very carefully taking into consideration layout factors to consider, boosting casting performance, applying top quality control procedures, and maximizing profitability, manufacturers can open the complete capacity of light weight aluminum casting.